By definition, multiphase flow is the interactive flow of two or more distinct phases with common interfaces in, say, a conduit. Each phase, representing a volume fraction (or mass fraction) of solid, liquid, or gaseous matter, has its own properties, velocity, and temperature.
A multiphase flow can be a simultaneous flow of:
- Materials with different states or phases (e.g.,, water-steam mixture).
- Materials with different chemical properties but in the same state or phase (e.g.,, oil droplets in water).
There are many combinations in industrial processes, but the most common being the simultaneous flow of steam and liquid water (as encountered in steam generators and condensers). In reactor engineering, a great deal of study has been performed on the nature of two-phase flow in case of a loss-of-coolant accident (LOCA), an accident of importance in reactor safety, and all thermal-hydraulic analyses (DNBR analyses).
Characteristics of Two-phase Fluid Flow
All two-phase flow problems have features that are characteristically different from those found in single-phase problems.
- In the case of steam and liquid water, the density of the two phases differs by a factor of about 1000. Therefore the influence of gravitational body force on multiphase flows is of much greater importance than in the case of single-phase flows.
- The sound speed changes dramatically for materials undergoing a phase change and can be orders of magnitude different. This significantly influences a flow through an orifice.
- The relative concentration of different phases is usually a dependent parameter of great importance in multiphase flows, while it is a parameter of no consequence in single-phase flows.
- The phase change means flow-induced pressure drops can cause further phase change (e.g.,, water can evaporate through an orifice), increasing the relative volume of the gaseous, compressible medium and increasing efflux velocities, unlike single-phase incompressible flow where decreasing of an orifice would decrease efflux velocities.
- The spatial distribution of the various phases in the flow channel strongly affects the flow behavior.
- There are many types of instabilities in multiphase flow.
Basic Parameters of Two‐phase Fluid Flow
This section will consider the simultaneous flow of gas (or vapor) and liquid water (as encountered in steam generators and condensers) in concurrent flow through a duct with cross-sectional area A. The subscripts “v” and “ℓ” indicate the vapor and liquid phase, respectively. Fundamental parameters that characterize this flow are:
Flow Patterns – Two-phase Flow
One of the most challenging aspects of dealing with the two-phase flow or multiphase flow is the fact that it can take many different forms. Spatial distributions and velocities of the liquid and vapor phases in the flow channel are very important aspects in many engineering branches. Pressure drops and heat transfer coefficients strongly depend on the local flow structure, and thus it is important in the engineering of nuclear reactors. The observed flow structures are defined as two-phase flow patterns, and these have particular identifying characteristics. These different flow patterns have been categorized according to the direction of flow relative to gravitational acceleration.
- Flow patterns in vertical tubes
- Flow patterns in horizontal tubes
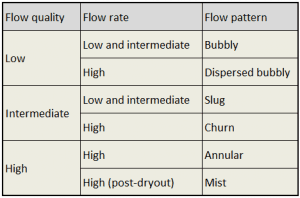
The main flow regimes in vertical tubes are shown in the table. It must be noted values of flow quality and flow rate is dependent on the fluid and pressure. In horizontal tubes, there can also be stratified flow (especially at low flow rates), at which the two phases separate under the effect of gravity.
The vapor/gas phase tends to be distributed as small bubbles at low vapor flow rates for a constant liquid flow rate. Increasing void fraction causes the agglomeration of bubbles into larger plugs and slugs. Further agglomeration of slugs, caused by further increasing void fraction, causes separation of the phases into annular patterns wherein liquid concentrates at the channel wall, and vapor flows in the central core of the vertical channel.
For horizontal channels, gravitational force tends to drain the liquid annulus toward the bottom of the channel, resulting in stratified flow. The gravitational force acting on the liquid phase can be overcome by kinetic forces at high flow rates, causing stratified flows to revert to annular flows. At very high flow rates, the annular film is thinned by the shear of the vapor core, and all the liquid is entrained as droplets in the vapor phase. This flow regime is usually known as the mist flow.
See also: Engineering Data Book III, Thome, J.R., Wolverine Tube Inc, 2004.
Flow Patterns – Vertical Tubes
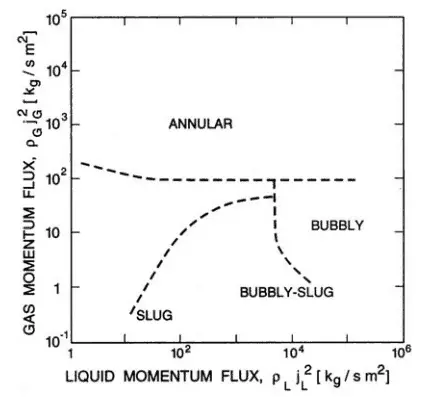
Flow Patterns – Horizontal Tubes
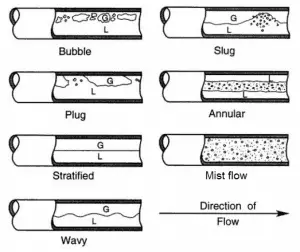

Flow patterns during evaporation
The previous section describes various flow patterns and shortly describes their behavior. These flow patterns were considered to be at constant void fraction and constant superficial velocities. But many industrial applications have to consider a variable void fraction and variable superficial velocities. In the nuclear industry, we have to deal with flow patterns during evaporation (i.e., during changes in the void fraction).
Detailed knowledge of phase changes and the behavior of the flow during the phase change is one of the most important considerations in the design of a nuclear reactor, especially in the following applications:
BWR – Boiling Water Reactors
- A boiling water reactor is cooled and moderated by water like a PWR, but at a lower pressure (7MPa), which allows the water to boil inside the pressure vessel producing the steam that runs the turbines. Evaporation, therefore, occurs directly in fuel channels. Therefore, BWRs are the best example for this area because coolant evaporation occurs at normal operation and is a very desired phenomenon.
- In BWRs, there is a phenomenon that is of the highest importance in reactor safety. This phenomenon is known as the “dry out” and is directly associated with changes in flow pattern during evaporation. At normal, the fuel surface is effectively cooled by boiling coolant. However, when the heat flux exceeds a critical value (CHF – critical heat flux), the flow pattern may reach the dry-out conditions (a thin film of liquid disappears). The heat transfer from the fuel surface into the coolant is deteriorated due to a drastically increased fuel surface temperature.
- PWR – Pressurized Water Reactors
- In PWRs at normal operation, the flow is considered to be single-phase. But a great deal of study has been performed on the nature of two-phase flow in case of transients and accidents (such as the loss-of-coolant accident – LOCA or trip of RCPs), which are of importance in reactor safety and in must be proved and declared in the Safety Analysis Report (SAR). In the case of PWRs, the problematic phenomenon is not the dry out. In the case of PWRs, the critical flow is an inverted annular flow. This flow occurs when a fuel rod cladding surface is overheated, which causes the formation of a local vapor layer, causing a dramatic reduction in heat transfer capability. This phenomenon is known as a departure from nucleate boiling – DNB. The difference in flow regime between post-dry outflow and post-DNB flow is depicted in the figure.
- In PWRs, evaporation also occurs in steam generators. Steam generators are heat exchangers that convert feedwater into steam from heat produced in a nuclear reactor core. The steam produced drives the turbine.
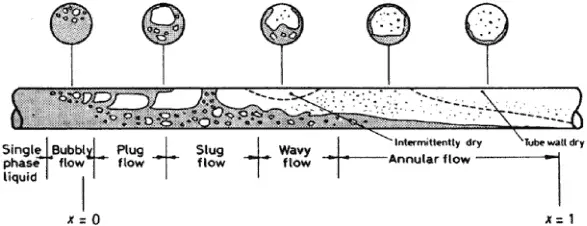
Two-phase Pressure Drop
In the practical analysis of piping systems, the quantity of most importance is the pressure loss due to viscous effects along the length of the system, as well as additional pressure losses arising from other technological equipments like valves, elbows, piping entrances, fittings, and tees.
In contrast, to single-phase pressure drops, calculation and prediction of two-phase pressure drops is a much more complex problem, and leading methods differ significantly. Experimental data indicates that the frictional pressure drop in the two-phase flow (e.g.,, in a boiling channel) is substantially higher than for a single-phase flow with the same length and mass flow rate. Explanations include an apparently increased surface roughness due to bubble formation on the heated surface and increased flow velocities.
Pressure Drop – Homogeneous Flow Model
The simplest approach to predicting two-phase flows is to treat the entire two-phase flow as if it were all liquid, except flowing at the two-phase mixture velocity. The two-phase pressure drops for flows inside pipes and channels are the sum of three contributions:
- the static pressure drop ∆pstatic (elevation head)
- the momentum pressure drop ∆pmom (fluid acceleration)
- the frictional pressure drop ∆pfrict
The total pressure drop of the two-phase flow is then:
∆ptotal = ∆pstatic + ∆pmom + ∆pfrict
The static and momentum pressure drops can be calculated similarly as in the case of single-phase flow and using the homogeneous mixture density:
The most problematic term is the frictional pressure drop ∆pfrict, which is based on the single-phase pressure drop multiplied by the two-phase correction factor (homogeneous friction multiplier – Φlo2). By this approach, the frictional component of the two-phase pressure drop is:
where (dP/dz)2f is frictional pressure gradient of two-phase flow and (dP/dz)1f is frictional pressure gradient if an entire flow (of total mass flow rate G) flows like a liquid in the channel (standard single-phase pressure drop). The term Φlo2 is the homogeneous friction multiplier that can be derived according to various methods. One of the possible multipliers is equal to Φlo2 = (1+xg(ρl/ρg – 1)) and therefore:
As can be seen, this simple model suggests that the two-phase frictional losses are in any event higher than the single-phase frictional losses. The homogeneous friction multiplier increases rapidly with flow quality.
Typical flow qualities in steam generators and BWR cores are on the order of 10 to 20 %. The corresponding two-phase frictional loss would be 2 – 4 times that in an equivalent single-phase system.
Flow Instability
In general, there are many instabilities that may occur in two-phase systems. In nuclear engineering, the study of the multiphase flow stability is important in the accident management of pressurized water reactors and the highest importance in normal/abnormal conditions in boiling water reactors.
In PWRs at normal operation, the flow is considered to be single-phase. But a great deal of study has been performed on the flow instability in case of transients and accidents (such as the loss-of-coolant accident – LOCA or trip of RCPs with the presence of natural circulation), in which flow oscillations or flow reversals may occur.
Flow oscillations are variations in flow caused by void formations, which are undesirable for several reasons.
- Flow oscillations can cause undesirable mechanical stress on fuel components (such as spacing grids). This can lead to the failure of those components due to fatigue.
- Flow oscillations affect the local heat transfer characteristics. In the case of PWRs, the critical safety issue is named DNB (departure from nucleate boiling), which causes the formation of a local vapor layer, causing a dramatic reduction in heat transfer capability. It has been found through testing that the critical heat flux (CHF) required for departure from nucleate boiling (DNB) can be lowered by as much as 40% when the flow is oscillating. This severely reduces the thermal limit and the power density along the length of the reactor core.
Flow oscillations can be a problem during natural circulation operations (e.g.,, after tripping of all RCPs). Natural circulation is an important design feature and ultimate heat removal mechanism. Because of the low flow rates present, coolant boiling may occur, which may form flow oscillations. During natural circulation, the steam bubbles formed during a flow oscillation may have enough effect to actually cause complete flow reversal in the affected channel.
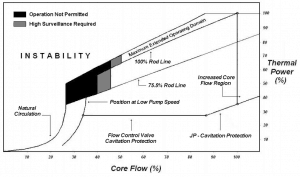
In BWRs, evaporation of coolant occurs at normal operation, and it is a very desired phenomenon. On the other hand, convective evaporation in the fuel channel causes that the flow pattern changes along the fuel channel depending on the flow rate and thermal power. It has been found that there are instability regions in which two-phase flow instabilities may arise. These two-phase flow instabilities are undesirable as they can result in mechanical vibrations and system control problems, affect normal operation, restrict operating parameters, and influence reactor safety. It must be noted flow stability in BWRs is not a major issue for many years because it is a well-known phenomenon.
In general, there are many classifications of flow instabilities. The following classification is based upon thermal-hydraulic fundamental mechanisms:
The static instabilities are:
- Flow excursion
- Boiling crisis
- Relaxation types, including flow pattern transition
The dynamic instabilities are:
- Density wave oscillations
- Pressure drop oscillations
- Thermal oscillations.
The proper characterization of the instabilities and the condition for their occurrence can determine the optimal and safe operation of the systems. The most accepted explanation for the occurrence of the dynamic type of instabilities is called density wave oscillations (DWO).
The density wave causes a delay in the local pressure drop caused by a change in inlet flow. Because of this delay, the sum of all local pressure drops may result in a total drop that is out-of-phase with the inlet flow. The basic mechanism causing flow instabilities in BWRs is the density wave. The characteristic periods of these oscillations are associated with the time required for a fluid particle to travel through the entire loop.
Types of instabilities observed in BWRs
- Control System Instabilities. Control system instabilities are related to the action of controllers that, through actuators, attempt to regulate some of the variables of the reactor.
- Channel Flow Instabilities. This type of instability can be described as follows: Let assume a flow perturbation. This perturbation causes a “wave” of voids traveling upward through the channel, producing a two-phase pressure drop (pressure drop increases significantly as void fraction increases) that is delayed with respect to the original perturbation. An increase in channel pressure drop (density wave) may lead to instability in the flow rate.
- Coupled Neutronic-Thermohydraulic Instability. The dominant type of instabilities in commercial BWRs is the coupled neutronic-thermohydraulic instability (also known as reactivity instability). The power generation in BWRs is directly related to the fuel neutron flux, which is strongly related to the average void fraction in the core channels. This effect is known as reactivity feedback. The reactivity feedback caused by changes in void fraction (void coefficient) is delayed as the voids travel upward through the fuel channel. In some cases, the delay may be long enough, and the void feedback may be strong enough that the reactor configuration becomes unstable. In this case, the neutron flux may oscillate.
Special References:
- Francesco D’Auria, The BWR Stability Issue, THICKET 2008 – Session IX – Paper 26
- Dag Strømsvåg, Fundamental mechanisms of density wave oscillations and the effect of subcooling, NTNU, 2011.
- J. March-Leuba, Density -Wave Instabilities in Boiling Water Reactors. NUREG/CR-6003, ORNL, 1992.