One of the most challenging aspects of dealing with the two-phase flow or multi-phase flow is that it can take many different forms. Spatial distributions and velocities of the liquid and vapor phases in the flow channel is a very important aspect in many engineering branches. Pressure drops and heat transfer coefficients strongly depend on the local flow structure, and thus it is important in the engineering of nuclear reactors. The observed flow structures are defined as two-phase flow patterns, and these have particular identifying characteristics. These different flow patterns have been categorized according to the direction of flow relative to gravitational acceleration.
- Flow patterns in vertical tubes
- Flow patterns in horizontal tubes
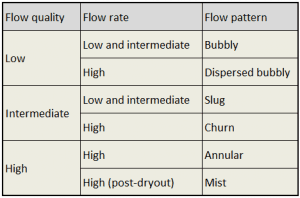
The main flow regimes in vertical tubes are shown in the table. It must be noted that flow quality values and flow rate depend on the fluid and pressure. In horizontal tubes, there can also be stratified flow (especially at low flow rates), at which the two phases separate under the effect of gravity.
The vapor/gas phase tends to be distributed as small bubbles at low vapor flow rates for a constant liquid flow rate. Increasing void fraction causes the agglomeration of bubbles into larger plugs and slugs. Further agglomeration of slugs, caused by further increasing void fraction, causes separation of the phases into annular patterns wherein liquid concentrates at the channel wall, and vapor flows in the central core of the vertical channel.
For horizontal channels, gravitational force tends to drain the liquid annulus toward the bottom of the channel, resulting in stratified flow. The gravitational force acting on the liquid phase can be overcome by kinetic forces at high flow rates, causing stratified flows to revert to annular flows. At very high flow rates, the annular film is thinned by the shear of the vapor core, and all the liquid is entrained as droplets in the vapor phase. This flow regime is usually known as the mist flow.
See also: Engineering Data Book III, Thome, J.R., Wolverine Tube Inc, 2004.
Flow Patterns – Vertical Tubes
Flow Patterns – Horizontal Tubes

Flow patterns during evaporation
The previous section describes various flow patterns and shortly describes their behavior. These flow patterns were considered to be at constant void fraction and constant superficial velocities. But many industrial applications have to consider a variable void fraction and variable superficial velocities. In the nuclear industry, we have to deal with flow patterns during evaporation (i.e., during changes in the void fraction).
Detailed knowledge of phase changes and the behavior of the flow during the phase change is one of the most important considerations in the design of a nuclear reactor, especially in the following applications:
BWR – Boiling Water Reactors
- A boiling water reactor is cooled and moderated by water like a PWR, but at a lower pressure (7MPa), which allows the water to boil inside the pressure vessel producing the steam that runs the turbines. Evaporation, therefore, occurs directly in fuel channels. Therefore BWRs are the best example for this area because coolant evaporation occurs at normal operation, and it is a very desired phenomenon.
- In BWRs, there is a phenomenon that is of the highest importance in reactor safety. This phenomenon is known as the “dry out” and is directly associated with changes in flow pattern during evaporation. At normal, the fuel surface is effectively cooled by boiling coolant. However, when the heat flux exceeds a critical value (CHF – critical heat flux), the flow pattern may reach the dry-out conditions (a thin film of liquid disappears). The heat transfer from the fuel surface into the coolant is deteriorated due to a drastically increased fuel surface temperature.
- PWR – Pressurized Water Reactors
- In PWRs at normal operation, the flow is considered to be single-phase. But a great deal of study has been performed on the nature of two-phase flow in case of transients and accidents (such as the loss-of-coolant accident – LOCA or trip of RCPs), which are of importance in reactor safety and in must be proved and declared in the Safety Analysis Report (SAR). In the case of PWRs, the problematic phenomenon is not the dry out. In the case of PWRs, the critical flow is an inverted annular flow. This flow occurs when a fuel rod cladding surface is overheated, which causes the formation of a local vapor layer, causing a dramatic reduction in heat transfer capability. This phenomenon is known as a departure from nucleate boiling – DNB. The difference in flow regime between post-dry outflow and post-DNB flow is depicted in the figure.
- In PWRs, evaporation also occurs in steam generators. Steam generators are heat exchangers that convert feedwater into steam from heat produced in a nuclear reactor core. The steam produced drives the turbine.