
Pure zirconium is a lustrous, grey-white, strong transition metal that resembles hafnium and titanium to a lesser extent. Zirconium is mainly used as a refractory and opacifier, although small amounts are used as an alloying agent for its strong corrosion resistance. Zirconium and its alloys are widely used as a cladding for nuclear reactor fuels. Zirconium alloyed with niobium or tin has excellent corrosion properties. The high corrosion resistance of zirconium alloys results from the natural formation of a dense stable oxide on the surface of the metal. This film is self-healing. It grows slowly at temperatures up to approximately 550 °C (1020 °F) and remains tightly adherent. The desired property of these alloys is also a low neutron-capture cross-section. The disadvantages of zirconium are low strength properties and low heat resistance, which can be eliminated, for example, by alloying with niobium.
- Zirconium – Niobium Alloys. Zirconium alloys with niobium are used as claddings of fuel elements of VVER and RBMK reactors. These alloys are the basic material of the assembly channel of the RBMK reactor. The Zr + 1% Nb alloy of type N-1 E-110 is used for fuel element claddings, and the Zr + 2.5% Nb alloy of type E-125 is applied for tubes of assembly channels.
- Zirconium – Tin Alloys. Zirconium alloys, in which tin is the basic alloying element, provide improvement of their mechanical properties and have a wide distribution in the USA. A common subgroup has the trademark Zircaloy. In the case of zirconium-tin alloys, the corrosion resistance in water and steam is decreased, resulting in the need for additional alloying.
The cladding material for the new 17×17 fuel designs is also based on the zirconium-niobium alloys (e.g., Optimized ZIRLO material), which have been demonstrated to have improved corrosion resistance compared with prior fuel cladding materials. The optimized tin level provides a reduced corrosion rate while maintaining the benefits of mechanical strength and resistance to accelerated corrosion from abnormal chemistry conditions.
Costs of Zirconium
In terms of cost, these alloys are often the materials of choice for heat exchangers and piping systems for the chemical-processing and nuclear industries. Zirconium is a by-product of the mining and processing of titanium minerals and tin mining. From 2003 to 2007, while prices for the mineral zircon steadily increased from $360 to $840 per tonne, the price for unwrought zirconium metal decreased from $39,900 to $22,700 per ton. Zirconium metal is much more expensive than zircon because the reduction processes are costly. All costs significantly vary with certain purity.
Production of Zirconium
The production of zirconium metal requires special techniques due to the particular chemical properties of zirconium. Most Zr metal is produced from zircon (ZrSiO4) by reducing the zirconium chloride with magnesium metal in the Kroll process. The key feature of the Kroll process is the reduction of zirconium chloride to metallic zirconium by magnesium. Commercial non-nuclear grade zirconium typically contains 1–5% of hafnium, whose neutron absorption cross-section is 600x that of zirconium. Hafnium must be almost entirely removed (reduced to < 0.02% of the alloy) for reactor applications.
Zirconium Alloys in Nuclear Industry
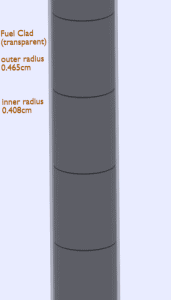
Fuel cladding is the outer layer of the fuel rods, standing between the reactor coolant and the nuclear fuel (i.e., fuel pellets). It is made of corrosion-resistant material with a low absorption cross section for thermal neutrons (~ 0.18 × 10–24 cm2), usually zirconium alloy. The fuel cladding typically has an inner radius of rZr,2 = 0.408 cm and outer radius rZr,1 = 0.465 cm. Compared to the fuel pellet, there is almost no heat generation in the fuel cladding (cladding is slightly heated by radiation). All heat generated in the fuel must be transferred via conduction through the cladding; therefore, the inner surface is hotter than the outer surface.
A typical composition of nuclear-grade zirconium alloys is more than 95 percent zirconium and less than 2% of tin, niobium, iron, chromium, nickel, and other metals, which are added to improve mechanical properties and corrosion resistance. To date, the most commonly used alloy in PWRs has been Zircaloy 4. However, currently, this is being replaced by new zirconium–niobium-based alloys, exhibiting better corrosion resistance. The maximum temperature at which zirconium alloys can be used in water-cooled reactors depends on their corrosion resistance. The most common zirconium alloys, Zircaloy-2 and Zircaloy-4, contain the strong α stabilizers tin and oxygen, plus the β stabilizers iron, chromium, and nickel. Alloys of type Zircalloy, in which tin is the basic alloying element that improves their mechanical properties, have a wide distribution worldwide. However, in this case, the decrease of corrosion resistance in water and steam is taken place, resulting in the need for additional alloying. The improvement brought about by the additive niobium probably involves a different mechanism. The high corrosion resistance of niobium alloyed metals in water and steam at temperatures of 400–550°C is caused by their ability to passivation with the formation of protective films.
Oxidation of Zirconium Alloys
The oxidation of zirconium alloys is one of the most studied processes in the nuclear industry. The oxidative reaction of zirconium with water releases hydrogen gas, which partly diffuses into the alloy and forms zirconium hydrides. The hydrides are less dense and are weaker mechanically than the alloy; their formation results in blistering and cracking of the cladding – a phenomenon known as hydrogen embrittlement. While many of these reports are written to address the reaction of fuel and steam with zirconium alloys in the case of a nuclear accident, there are still a substantial number of reports dealing with the oxidation of zirconium alloys at moderate temperatures of about 800 K and below.
Zr + 2H2O→ZrO2 + 2H2
At high temperatures, the exothermic reaction of Zr-base alloys with steam is much more intensive and hazardous for the safety of nuclear power plants during accidents like a loss-of-coolant accident (LOCA). The main problem of high-temperature oxidation is that zirconium cladding rapidly reacts with water steam at high temperatures. The oxidation kinetics of relevant zirconium alloys appears to be parabolic in the temperature range of 1000-1500°C for many Zr-based alloys.
Zirconium Alloy – Zircaloy – 4
Zircaloy-4 (UNS R60804) is a variation of Zircaloy-2, but it contains no nickel and has a higher, more closely controlled iron content. Mechanical properties are similar to pure zirconium, stronger and less ductile, with excellent corrosion resistance. This alloy is also used in nuclear service; it absorbs less hydrogen than Zircaloy-2 when exposed to corrosion in water and steam.
Zircaloy-4 was developed from Zircaloy-2 with the principal aim of reducing the tendency to pick up hydrogen. Thus, the same composition specifications are applicable, except for nickel, which is limited to a maximum of 0.007%, and iron, the range of which is reduced to 0.18%.
Hydrogen Embrittlement of Zirconium Alloys
See also: Hydrogen Embrittlement
Cladding prevents radioactive fission products from escaping the fuel matrix into the reactor coolant and contaminating it. There are various fuel failure root causes, that have been identified in the past. These causes were predominantly fabrication defects or fretting in the early days of PWR and BWR operations. One possible cause is also:
- Internal Hydriding. Inadvertent inclusion of hydrogen-containing materials inside a fuel rod can result in hydriding and thus embrittlement fuel cladding. Hydrogen sources were mainly residual moisture or organic contamination in fuel pellets/rods. This cause of failure has been practically eliminated through improved manufacturing.
- Delayed hydride cracking (DHC). Delayed hydride cracking is time-dependent crack initiation and propagation through fracture of hydrides that can form ahead of the crack tip. This type of failure can be initiated by long cracks at the outer surface of the cladding, which can propagate in an axial/radial direction. This failure mechanism may potentially limit high burnup operation.
Properties of Zirconium Alloy – Zircaloy – 4
Material properties are intensive properties, which means they are independent of the amount of mass and may vary from place to place within the system at any moment. Materials science involves studying materials’ structure and relating them to their properties (mechanical, electrical, etc.). Once materials scientist knows about this structure-property correlation, they can then go on to study the relative performance of a material in a given application. The major determinants of the structure of a material and, thus, its properties are its constituent chemical elements and how it has been processed into its final form.
The density of Zirconium Alloy – Zircaloy – 4
Density of typical zirconium alloy is 6.6 g/cm3 (0.24 lb/in3).
Density is defined as the mass per unit volume. It is an intensive property, which is mathematically defined as mass divided by volume:
ρ = m/V
In words, the density (ρ) of a substance is the total mass (m) of that substance divided by the total volume (V) occupied by that substance. The standard SI unit is kilograms per cubic meter (kg/m3). The Standard English unit is pounds mass per cubic foot (lbm/ft3).
Since the density (ρ) of a substance is the total mass (m) of that substance divided by the total volume (V) occupied by that substance, it is obvious that the density of a substance strongly depends on its atomic mass and also on the atomic number density (N; atoms/cm3),
- Atomic Weight. The atomic mass is carried by the atomic nucleus, which occupies only about 10-12 of the atom’s total volume or less, but it contains all the positive charge and at least 99.95% of the atom’s total mass. Therefore it is determined by the mass number (number of protons and neutrons).
- Atomic Number Density. The atomic number density (N; atoms/cm3), which is associated with atomic radii, is the number of atoms of a given type per unit volume (V; cm3) of the material. The atomic number density (N; atoms/cm3) of a pure material having an atomic or molecular weight (M; grams/mol) and the material density (⍴; gram/cm3) is easily computed from the following equation using Avogadro’s number (NA = 6.022×1023 atoms or molecules per mole):
- Crystal Structure. The density of a crystalline substance is significantly affected by its crystal structure. FCC structure, along with its hexagonal relative (hcp), has the most efficient packing factor (74%). Metals containing FCC structures include austenite, aluminum, copper, lead, silver, gold, nickel, platinum, and thorium.
Mechanical Properties of Zirconium Alloy – Zircaloy – 4
Materials are frequently chosen for various applications because they have desirable combinations of mechanical characteristics. For structural applications, material properties are crucial, and engineers must consider them.
Strength of Zirconium Alloy – Zircaloy – 4
In the mechanics of materials, the strength of a material is its ability to withstand an applied load without failure or plastic deformation. The strength of materials considers the relationship between the external loads applied to a material and the resulting deformation or change in material dimensions. The strength of a material is its ability to withstand this applied load without failure or plastic deformation.
Ultimate Tensile Strength
The ultimate tensile strength of zirconium alloy – Zircaloy – 4 is about 514 MPa.
The ultimate tensile strength is the maximum on the engineering stress-strain curve. This corresponds to the maximum stress that a structure in tension can sustain. Ultimate tensile strength is often shortened to “tensile strength” or “the ultimate.” If this stress is applied and maintained, the fracture will result. Often, this value is significantly more than the yield stress (as much as 50 to 60 percent more than the yield for some types of metals). When a ductile material reaches its ultimate strength, it experiences necking where the cross-sectional area reduces locally. The stress-strain curve contains no higher stress than the ultimate strength. Even though deformations can continue to increase, the stress usually decreases after achieving the ultimate strength. It is an intensive property; therefore its value does not depend on the size of the test specimen. However, it depends on other factors, such as the specimen preparation, the presence or otherwise of surface defects, and the temperature of the test environment and material. Ultimate tensile strengths vary from 50 MPa for aluminum to as high as 3000 MPa for high-strength steel.
Yield Strength
The yield strength of zirconium alloy – Zircaloy – 4 is about 381 MPa.
The yield point is the point on a stress-strain curve that indicates the limit of elastic behavior and the beginning plastic behavior. Yield strength or yield stress is the material property defined as the stress at which a material begins to deform plastically. In contrast, the yield point is where nonlinear (elastic + plastic) deformation begins. Before the yield point, the material will deform elastically and return to its original shape when the applied stress is removed. Once the yield point is passed, some fraction of the deformation will be permanent and non-reversible. Some steels and other materials exhibit a behavior termed a yield point phenomenon. Yield strengths vary from 35 MPa for low-strength aluminum to greater than 1400 MPa for high-strength steel.
Young’s Modulus of Elasticity
Young’s modulus of elasticity of zirconium alloy – Zircaloy – 4 is about 99 GPa.
Young’s modulus of elasticity is the elastic modulus for tensile and compressive stress in the linear elasticity regime of a uniaxial deformation and is usually assessed by tensile tests. Up to limiting stress, a body will be able to recover its dimensions on the removal of the load. The applied stresses cause the atoms in a crystal to move from their equilibrium position, and all the atoms are displaced the same amount and maintain their relative geometry. When the stresses are removed, all the atoms return to their original positions, and no permanent deformation occurs. According to Hooke’s law, the stress is proportional to the strain (in the elastic region), and the slope is Young’s modulus. Young’s modulus is equal to the longitudinal stress divided by the strain.
The hardness of Zirconium Alloy – Zircaloy – 4
Rockwell hardness of zirconium alloy – Zircaloy – 4 is approximately 89 HRB.
Rockwell hardness test is one of the most common indentation hardness tests, that has been developed for hardness testing. In contrast to the Brinell test, the Rockwell tester measures the depth of penetration of an indenter under a large load (major load) compared to the penetration made by a preload (minor load). The minor load establishes the zero position, and the major load is applied and removed while maintaining the minor load. The difference between the penetration depth before and after applying the major load is used to calculate the Rockwell hardness number. That is, the penetration depth and hardness are inversely proportional. The chief advantage of Rockwell hardness is its ability to display hardness values directly. The result is a dimensionless number noted as HRA, HRB, HRC, etc., where the last letter is the respective Rockwell scale.
The Rockwell C test is performed with a Brale penetrator (120°diamond cone) and a major load of 150kg.
Thermal Properties of Zirconium Alloy – Zircaloy – 4
Thermal properties of materials refer to the response of materials to changes in their temperature and the application of heat. As a solid absorbs energy in the form of heat, its temperature rises, and its dimensions increase. But different materials react to the application of heat differently.
Heat capacity, thermal expansion, and thermal conductivity are often critical in solids’ practical use.
Melting Point of Zirconium Alloy – Zircaloy – 4
The melting point of zirconium alloy – Zircaloy – 4 is around 1850°C.
In general, melting is a phase change of a substance from the solid to the liquid phase. The melting point of a substance is the temperature at which this phase change occurs. The melting point also defines a condition where the solid and liquid can exist in equilibrium.
Thermal Conductivity of Zirconium Alloy – Zircaloy – 4
Zirconium alloys have lower thermal conductivity (about 18 W/m.K) than pure zirconium metal (about 22 W/m.K).
The heat transfer characteristics of solid material are measured by a property called the thermal conductivity, k (or λ), measured in W/m.K. It measures a substance’s ability to transfer heat through a material by conduction. Note that Fourier’s law applies to all matter, regardless of its state (solid, liquid, or gas), therefore, it is also defined for liquids and gases.
The thermal conductivity of most liquids and solids varies with temperature, and for vapors, it also depends upon pressure. In general:
Most materials are nearly homogeneous, therefore, we can usually write k = k (T). Similar definitions are associated with thermal conductivities in the y- and z-directions (ky, kz), but for an isotropic material the thermal conductivity is independent of the direction of transfer, kx = ky = kz = k.