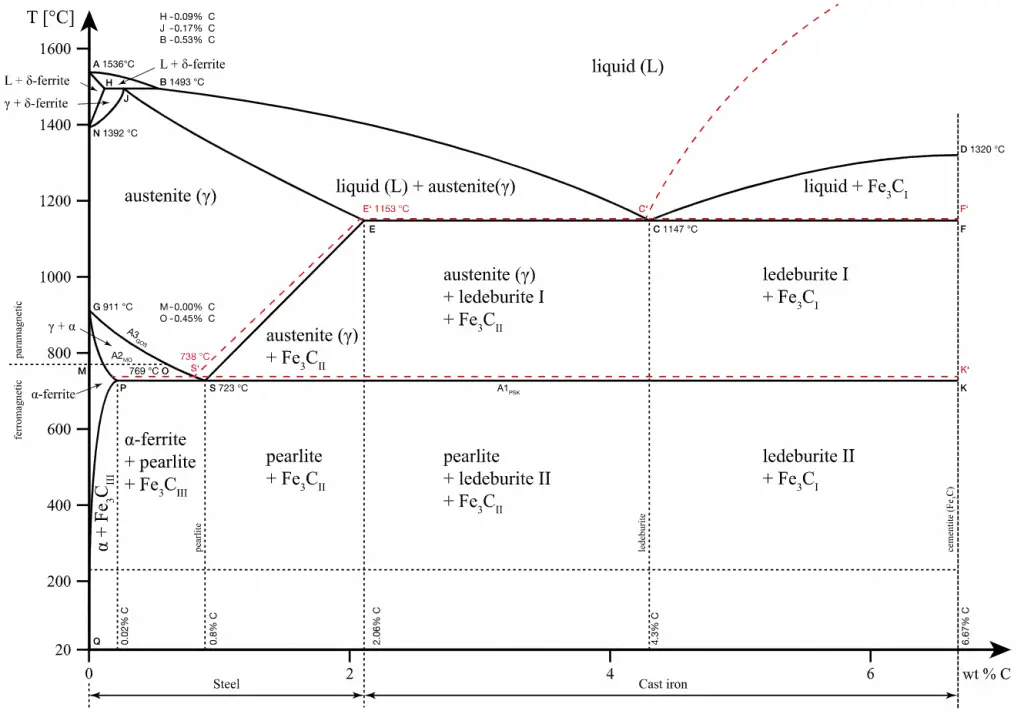
Steels are iron-carbon alloys that may contain appreciable concentrations of other alloying elements. Adding a small amount of non-metallic carbon to iron trades its great ductility for greater strength. Due to its very-high strength but still substantial toughness, and its ability to be greatly altered by heat treatment, steel is one of the most useful and common ferrous alloys in modern use. Thousands of alloys have different compositions and/or heat treatments. The mechanical properties are sensitive to carbon content, which is normally less than 1.0 wt%. According to our AISI classification, carbon steel is divided into four classes based on carbon content.
Characteristics of Metal Alloys
Alloys are usually stronger than pure metals, although they generally offer reduced electrical and thermal conductivity. Strength is the most important criterion by which many structural materials are judged. Therefore, alloys are used for engineering construction. Steel, probably the most common structural metal, is a good example of an alloy. It is an alloy of iron and carbon, with other elements to give it certain desirable properties.
It is sometimes possible for a material to be composed of several solid phases. The strengths of these materials are enhanced by allowing a solid structure to become a form composed of two interspersed phases. When the material in question is an alloy, it is possible to quench the metal from a molten state to form the interspersed phases. Quenching refers to a heat treatment in which a material is rapidly cooled in water, oil, or air to obtain certain material properties, especially hardness. In metallurgy, quenching is commonly used to harden steel by introducing martensite.
Ferrous Alloys
Ferrous alloys, in which iron is the principal constituent, include steel and pig iron (with a carbon content of a few percent) and alloys of iron with other metals (such as stainless steel). Ferrous alloys are known for their strength. Alloys are usually stronger than pure metals, although they generally offer reduced electrical and thermal conductivity. The simplest ferrous alloys are known as steels, and they consist of iron (Fe) alloyed with carbon (C) (about 0.1% to 1%, depending on the type). Adding a small amount of non-metallic carbon to iron trades its great ductility for greater strength. Due to its very-high strength but still substantial toughness, and its ability to be greatly altered by heat treatment, steel is one of the most useful and common ferrous alloys in modern use. Their widespread use is accounted for by the following factors:
- Iron-containing compounds exist in abundant quantities within the Earth’s crust.
- Metallic iron and steel alloys may be produced using relatively economical extraction, refining, alloying, and fabrication techniques.
- Ferrous alloys are extremely versatile in that they may be tailored to have a wide range of mechanical and physical properties.
The principal disadvantage of many ferrous alloys is their susceptibility to corrosion. By adding chromium to steel, its resistance to corrosion can be enhanced, creating stainless steel, while adding silicon will alter its electrical characteristics, producing silicon steel.
Types of Steels – Classification Based on Composition
-
Typical applications for low-carbon steel include automobile body components, structural shapes (e.g., I-beams, channel and angle iron), and sheets used in pipelines and buildings. Steel. Steels are iron-carbon alloys that may contain appreciable concentrations of other alloying elements. Adding a small amount of non-metallic carbon to iron trades its great ductility for greater strength. Due to its very-high strength but still substantial toughness, and its ability to be greatly altered by heat treatment, steel is one of the most useful and common ferrous alloys in modern use. Thousands of alloys have different compositions and/or heat treatments. The mechanical properties are sensitive to the content of carbon, which is normally less than 1.0 wt%. According to our AISI classification, carbon steel is broken down into four classes based on carbon content:
- Low-carbon Steels. Low-carbon steel, also known as mild steel, is now the most common form of steel because its price is relatively low. At the same time, it provides material properties that are acceptable for many applications. Low-carbon steel contains approximately 0.05–0.25% carbon making it malleable and ductile. Mild steel has a relatively low tensile strength, but it is cheap and easy to form; surface hardness can be increased through carburizing.
-
Medium-carbon steel is mostly used to produce machine components, shafts, axles, gears, crankshafts, coupling, and forgings. It could also be used in rails, railway wheels, other machine parts, and high-strength structural components calling for a combination of high strength, wear resistance, and toughness. Medium-carbon Steels. Medium-carbon steel has approximately 0.3–0.6% carbon content, balances ductility and strength, and has good wear resistance. This grade of steel is mostly used in the production of machine components, shafts, axles, gears, crankshafts, coupling, and forgings and could also be used in rails and railway wheels.
- High-carbon Steels. High-carbon steel has approximately 0.60 to 1.00% carbon content, and hardness is higher than in the other grades, but ductility decreases. High carbon steels could be used for springs, rope wires, hammers, screwdrivers, and wrenches.
- Ultra-high-carbon Steels. Ultra-high-carbon steel has approximately 1.25–2.0% carbon content. Steels that can be tempered to great hardness. This steel grade could be used for hard steel products, such as truck springs, metal cutting tools, and other special purposes like (non-industrial-purpose) knives, axles, or punches. Most steels with more than 2.5% carbon content are made using powder metallurgy.
- Alloy Steels. Steel is an alloy of iron and carbon. Still, the term alloy steel usually only refers to steels that contain other elements— like vanadium, molybdenum, or cobalt—in amounts sufficient to alter the properties of the base steel. In general, alloy steel is alloyed with various elements in total amounts between 1.0% and 50% by weight to improve its mechanical properties. Alloy steels are broken down into two groups:
- Low-alloy Steels.
- High-alloy Steels.
-
Steam Turbine Blade. Superalloys (typically face-centered cubic austenitic alloys) based on Co, Ni, and Fe can be engineered to be highly resistant to creep and have thus arisen as an ideal material in high-temperature environments. Source wikipedia.org License: CC BY-SA 3.0 Stainless Steel. Stainless steels are low-carbon steels with at least 10% chromium with or without other alloying elements. Strength and corrosion resistance often make it the material of choice in transportation and processing equipment, engine parts, and firearms. Chromium increases hardness, strength, and corrosion resistance. Nickel gives similar benefits but adds hardness without sacrificing ductility and toughness. It also reduces thermal expansion for better dimensional stability.
- Superalloys.
Special Ferrous Metals
- Tool Steels
- High-speed Steels
- Shock-resisting Steels
- Silver Steel
Properties of Steels
Strength of Steels
In the mechanics of materials, the strength of a material is its ability to withstand an applied load without failure or plastic deformation. The strength of materials considers the relationship between the external loads applied to a material and the resulting deformation or change in material dimensions. The strength of a material is its ability to withstand this applied load without failure or plastic deformation.
Ultimate Tensile Strength
The ultimate tensile strength is the maximum on the engineering stress-strain curve. This corresponds to the maximum stress sustained by a structure in tension. Ultimate tensile strength is often shortened to “tensile strength” or “the ultimate.” If this stress is applied and maintained, a fracture will result. Often, this value is significantly more than the yield stress (as much as 50 to 60 percent more than the yield for some types of metals). When a ductile material reaches its ultimate strength, it experiences necking where the cross-sectional area reduces locally. The stress-strain curve contains no higher stress than the ultimate strength. Even though deformations can continue to increase, the stress usually decreases after achieving the ultimate strength. It is an intensive property; therefore its value does not depend on the size of the test specimen. However, it depends on other factors, such as the preparation of the specimen, the presence or otherwise of surface defects, and the temperature of the test environment and material. Ultimate tensile strengths vary from 50 MPa for aluminum to as high as 3000 MPa for very high-strength steel.
Example – Ultimate Tensile Strength – Low-carbon Steel
The ultimate tensile strength of low-carbon steel is between 400 – 550 MPa.
Example – Ultimate Tensile Strength – Ultra-high-carbon Steel
The ultimate tensile strength of ultra-high-carbon steel is 1100 MPa.
Yield Strength
The yield point is the point on a stress-strain curve that indicates the limit of elastic behavior and the beginning plastic behavior. Yield strength or yield stress is the material property defined as the stress at which a material begins to deform plastically. In contrast, the yield point is where nonlinear (elastic + plastic) deformation begins. Before the yield point, the material will deform elastically and return to its original shape when the applied stress is removed. Once the yield point is passed, some fraction of the deformation will be permanent and non-reversible. Some steels and other materials exhibit a behavior termed a yield point phenomenon. Yield strengths vary from 35 MPa for low-strength aluminum to greater than 1400 MPa for high-strength steel.
Example – Yield Strength – Low-carbon Steel
The yield strength of low-carbon steel is 250 MPa.
Example – Yield Strength – Ultra-high-carbon Steel
The yield strength of ultra-high-carbon steel is 800 MPa.
Young’s Modulus of Elasticity
Young’s modulus of elasticity is the elastic modulus for tensile and compressive stress in the linear elasticity regime of a uniaxial deformation and is usually assessed by tensile tests. Up to limiting stress, a body will be able to recover its dimensions on the removal of the load. The applied stresses cause the atoms in a crystal to move from their equilibrium position, and all the atoms are displaced the same amount and maintain their relative geometry. When the stresses are removed, all the atoms return to their original positions and no permanent deformation occurs. According to Hooke’s law, the stress is proportional to the strain (in the elastic region), and the slope is Young’s modulus. Young’s modulus is equal to the longitudinal stress divided by the strain.
Example – Young’s modulus of elasticity – Low-carbon Steel
Young’s modulus of elasticity of low-carbon steel is 200 GPa.
Hardness of Steels
In materials science, hardness is the ability to withstand surface indentation (localized plastic deformation) and scratching. Hardness is probably the most poorly defined material property because it may indicate resistance to scratching, abrasion, indentation, or even resistance to shaping or localized plastic deformation. Hardness is important from an engineering standpoint because resistance to wear by either friction or erosion by steam, oil, and water generally increases with hardness.
Brinell hardness test is one of the indentation hardness tests developed for hardness testing. In Brinell tests, a hard, spherical indenter is forced under a specific load into the surface of the metal to be tested. The typical test uses a 10 mm (0.39 in) diameter hardened steel ball as an indenter with a 3,000 kgf (29.42 kN; 6,614 lbf) force. The load is maintained constant for a specified time (between 10 and 30 s). For softer materials, a smaller force is used; for harder materials, a tungsten carbide ball is substituted for the steel ball.
The test provides numerical results to quantify the hardness of a material, which is expressed by the Brinell hardness number – HB. The Brinell hardness number is designated by the most commonly used test standards (ASTM E10-14[2] and ISO 6506–1:2005) as HBW (H from hardness, B from Brinell, and W from the material of the indenter, tungsten (wolfram) carbide). In former standards, HB or HBS were used to refer to measurements made with steel indenters.
The Brinell hardness number (HB) is the load divided by the surface area of the indentation. The diameter of the impression is measured with a microscope with a superimposed scale. The Brinell hardness number is computed from the equation:
There are various test methods in common use (e.g., Brinell, Knoop, Vickers, and Rockwell). Some tables correlate the hardness numbers from the different test methods where correlation is applicable. In all scales, a high hardness number represents a hard metal.
Example – Hardness of Low-carbon Steel
Brinell hardness of low-carbon steel is approximately 120 MPa.
Example – Hardness of High-carbon Steel
Brinell hardness of high-carbon steel is approximately 200 MPa.
Example – Hardness of Damascus Steel
Rockwell hardness of Damascus steel depends on the current type of the steel, but it may be approximately 62-64 HRC Rockwell.