Accident tolerant fuels (ATF) are a series of new nuclear fuel concepts researched to improve fuel performance during normal operation, transient conditions, and accident scenarios, such as loss-of-coolant accidents (LOCA) or reactivity-initiated accidents (RIA). Following the Fukushima Daiichi accident, a fuel behavior review was initiated. Zirconium alloy clad fuel operates successfully to high burnup and is the result of 40 years of continuous development and improvement. However, under severe accident conditions, the high-temperature zirconium–steam interaction can be a major source of damage to the power plant.
These upgrades include:
- specially designed additives to standard fuel pellets intended to improve various properties and performance
- robust coatings applied to the outside of standard claddings intended to reduce corrosion, increase wear resistance, and reduce the production of hydrogen under high-temperature (accident) conditions
- development of completely new fuel designs with ceramic cladding and different fuel materials
Current fuel cladding is the outer layer of the fuel rods, standing between the reactor coolant and the nuclear fuel (i.e., fuel pellets). It is made of corrosion-resistant material with a low absorption cross section for thermal neutrons (~ 0.18 × 10–24 cm2), usually zirconium alloy. It prevents radioactive fission products from escaping the fuel matrix into the reactor coolant and contaminating it. Cladding constitutes one of the barriers to the ‘defence-in-depth ‘approach; therefore, its coolability is one of the key safety aspects.
Special Reference: Nuclear Energy Agency, State-of-the-Art Report on Light Water Reactor Accident-Tolerant Fuel. NEA No.7317, OECD, 2018.
Oxidation of Zirconium Alloys
The oxidation of zirconium alloys is one of the most studied processes in the nuclear industry. While many of these reports are written to address the reaction of fuel and steam with zirconium alloys in the case of a nuclear accident, there are still a substantial number of reports dealing with the oxidation of zirconium alloys at moderate temperatures of about 800 K and below. The aggressive agent in this respect is primary circuit water at a temperature of some 300° C. This oxidizes zirconium according to the reaction:
Zr + 2H2O→ZrO2 + 2H2
resulting in the formation of solid oxide on the metal’s surface. In summary, in the absence of neutron irradiation, the overall oxidation of zirconium and its alloys is fairly well understood. The oxidation rate depends upon the pressure of the oxygen or water vapor and scales approximately with pressure to 1/6th power. The dependence of oxidation rate R on temperature and pressure can be expressed as:
R = 13.9·P1/6·exp(−1.47/kBT)
The oxidation rate R is here expressed in gram/(cm2·second); P is the pressure in the atmosphere, that is, the factor P1/6 = 1 at ambient pressure; the activation energy is 1.47 eV; kB is the Boltzmann constant (8.617×10−5 eV/K), and T is the absolute temperature in kelvins.
The enhancement in the oxidation rate in the presence of fast neutrons depends upon neutron intensity, temperature, water chemistry, dissolved oxygen in the water, and oxide layer thickness. Part of the hydrogen thus generated is incorporated into the metallic matrix, migrating under the effect of the thermal gradient to accumulate in the less hot regions, forming hydrides that are liable to cause brittleness in the cladding as the fuel cools down. The two processes, oxidation and hydridation, are thus intimately bound together.
The most commonly used alloy in PWRs has been Zircaloy 4. However, currently, this is being replaced by new zirconium–niobium-based alloys, exhibiting better corrosion resistance. The maximum temperature at which zirconium alloys can be used in water-cooled reactors depends on their corrosion resistance. Alloys of type Zircalloy, in which tin is the basic alloying element that improves their mechanical properties, have a wide distribution worldwide. However, in this case, the decrease of corrosion resistance in water and steam is taken place, resulting in the need for additional alloying. The improvement brought about by the additive niobium probably involves a different mechanism. The high corrosion resistance of niobium alloyed metals in water and steam at temperatures of 400–550°C is caused by their ability to passivation with the formation of protective films.
At high temperatures, the exothermic reaction of Zr-base alloys with steam is much more intensive and hazardous for the safety of nuclear power plants during accidents like a loss-of-coolant accident (LOCA). The main problem of high-temperature oxidation is that zirconium cladding rapidly reacts with water steam at high temperatures. The oxidation kinetics of relevant zirconium alloys appears to be parabolic in the temperature range of 1000-1500°C for many Zr-based alloys. Above 1577°C, the oxide layer transforms from tetragonal to cubic, and the oxidation rate even increases. Moreover, the oxidation of zirconium by water is accompanied by a release of hydrogen gas. This oxidation is accelerated at high temperatures, e.g., inside a reactor core, if the fuel assemblies are no longer completely covered by liquid water and insufficiently cooled. Metallic zirconium is then oxidized by water/steam to form hydrogen gas according to the following redox reaction:
Zr + 2H2O→ZrO2 + 2H2 (Q = 190 kJ/mol; Baker and Just)
Above approximately 800°C, there is a phase transformation from the hexagonal (HCP) α-phase to the cubic β-phase (BCC). Oxygen, which diffuses into the remaining metal, stabilizes the α-phase. With cooling, the β phase will transform back to the α phase in which the oxygen concentration is significantly different from that of the oxygen-stabilized α and “prior β.” The problem is that these phase transitions make this material very brittle. Therefore, there are also three current LOCA licensing criteria (according to 10 CFR 50.46 – ECCS Acceptance Criteria for LWR) for preventing fuel failure (it can fail upon rewet during the introduction of emergency core cooling in a reactor accident or fail by overstraining under oxide cracks) due to oxygen and hydrogen embrittlement.
Advantages of Accident Tolerant Fuel
Accident tolerant fuel (ATF) can:
- endure the loss of active cooling in a reactor core for much longer than the current fuel
- widen the existing safety margin for nuclear plants
- improve nuclear plant performance with fuel that lasts longer
- reduce operational and maintenance costs to pass savings on to electricity consumers.
What is Coping Time
For a given accident scenario, the “fuel coping time” is the time lapse between departure from normal operation and the moment at which significant loss of geometry of the fuel assemblies occurs, such that the reactor core can no longer be cooled or the fuel cannot be removed from the reactor using currently available tools and procedures. Proposed ATF concepts seek to reduce severe accident (SA) risks by increasing the coping time available to operators for accident response, reducing the extent and rate of heat and hydrogen production from high-temperature (HT) steam oxidation, or reducing severe accident consequences by enhancing fission product (FP) retention.
Types of Accident Tolerant Fuels
Advanced Fuel Clad
While current nuclear fuel designs have operated very well under normal plant conditions, existing nuclear fuel designs can be challenged when put under beyond-design-basis severe-accident scenarios. In such conditions, the long-term loss of coolant and the resulting high temperatures of the fuel can lead to the degradation of the fuel cladding and the early release of fission products.
Proposed ATF concepts seek to reduce severe accident (SA) risks by increasing the coping time available to operators for accident response, reducing the extent and rate of heat and hydrogen production from high-temperature (HT) steam oxidation, or reducing severe accident consequences by enhancing fission product (FP) retention. The desired attributes for a practical ATF cladding material are quite rigorous. In addition to good material properties at high temperatures, the candidate material must be compatible with current fuel/core designs and provide economic operation, including good neutronics. Moreover, from an operational perspective, it must be highly reliable, have corrosion resistance, and exhibit low embrittlement at high burnups.
According to the NEA report, five different classes of cladding designs were the object of the review:
- Coated and improved Zr-alloys,
- Advanced steels,
- Refractory metals,
- SiC and SiC/SiC-composite claddings
- non-fuel components such as SiC/SiC channel boxes or accident-tolerant control rods (ATCR).
Advanced Fuel Pellets
According to the NEA report, the fuel designs covered by the Task Force on Advanced Fuel Designs consist of three different concepts:
- Improved UO2 fuel. Regarding the improved UO2 fuel, this design was divided into two sub-concepts: oxide-doped UO2 and high-thermal conductivity UO2 (designed by adding metallic or ceramic dopants).
- High-density fuel.
- Encapsulated fuel (TRISO-SiC-composite pellets).
Coated and improved Zr-alloys
Enhanced ATF concepts should either mitigate rapid waterside oxidation of the cladding during high-temperature transients in steam and/or steam/air mixture or reduce fuel temperature and fission gas release (FGR) during normal operation, improving the heat transport properties of the fuel. Thus the main goal for implementing coatings on the surface of zirconium alloy cladding was to provide a barrier to HT steam oxidation to significantly reduce the produced heat and hydrogen compared to uncoated zirconium alloys. Thus, the ideal ATF-cladding concept should have significantly reduced high-temperature steam oxidation kinetics leading to increased coping time relative to standard Zr-based alloys. The ideal ATF should also have higher mechanical strength at high temperatures to maintain coolable geometry.
The coatings studied thus far broadly fall within two categories:
- Metallic Coatings
- Cr-Coated Cladding. Cr-coated cladding and other metallic-coated claddings significantly reduce the high-temperature oxidation rates.
- Ceramic Coatings
Chromium-coated Fuel Cladding
Chromium is one of the possible coating elements for accident-tolerant fuel. Cr-coated zirconium cladding and other metallic-coated claddings significantly reduce the high-temperature oxidation rates. The coating thickness is usually between 20 and 30 mm. All investigated coating materials (Cr, FeCrAl, Cr-Al, CrN) are harder than zirconium alloys, so if the coating is sufficiently thick (> 30μm), then mechanical properties will be modified with increased strength and reduced ductility. The increased hardness of the coating materials has the benefit of potentially protecting the cladding against fretting and wear. Therefore Cr-coating may significantly reduce the risk of cladding damages due to debris or grid-to-rod fretting.
But the main advantage is that the coated cladding inherits all of the benefits of the base zirconium material properties but improves its oxidation and corrosion resistance for both normal operation and accident conditions. According to several investigations, Cr-coated cladding exhibits significantly increased post-quench strength and residual ductility. The strengthening effect of the Cr-coated cladding observed at high temperatures is beneficial in that it delays the time to rupture and better preserves the coolable geometry of the nuclear fuel channel by mitigating the flow blockage. Moreover, the corrosion of Cr-coated zirconium alloys is reduced to close to zero, thus also decreasing the hydrogen uptake by the cladding. The cladding will, therefore, not exhibit hydrogen embrittlement, leading to increased operating margins and potentially longer fuel rod irradiations.
Ceramic-coated Fuel Cladding
Ceramic coatings include oxides, carbides, nitrides, and composite or multilayer coatings. Nitride ceramic coatings harden materials and improve their wear behavior, especially TiN and TiAlN. Additionally, CrN is also used for corrosion protection. Ceramic coatings are much more brittle than metallic coatings and thus more likely to undergo cracking and damage. One of the main disadvantages of ceramic coatings is the dissolution of Al-containing coatings (TiAlN, CrAlN, and to a significantly lower extent FeCrAl).
Advanced Steels
FeCrAl alloys consist mainly of iron, chromium (20–30%), and aluminium (4–7.5 %). These alloys are known under the trademark Kanthal, a family of iron-chromium-aluminium (FeCrAl) alloys used in a wide range of resistance and high-temperature applications. FeCrAl is highly corrosion resistant due to forming a thin aluminum-rich oxide, Al2O3.
FeCrAl-based ATF utilizes a FeCrAl alloy material as fuel rod cladding in combination with uranium dioxide (UO2) fuel pellets. FeCrAl alloy clad fuel rods (with UO2 fuel) appear to exhibit properties that meet or exceed current fuel design technical requirements (with the exceptions noted below) while providing increased safety benefits during design-basis events and severe accident conditions. The concept’s key advantage over Zircaloy is its substantially slower oxidation kinetics up to 1773 K (1500°C). FeCrAl alloys have mechanical strength similar or superior to Zircaloy, with plastic yielding (ballooning) and perforation characteristics similar or better than zirconium alloys.
There are two main disadvantages of FeCrAl-based fuel clads:
- Increased parasitic neutron absorption. Due to increased neutron absorption cross-section of iron.
- Tritium releases. There is a potential increase in tritium release into the reactor coolant. Tritium is produced as a fission product (FP). FeCrAl does not react with hydrogen to form stable hydrides like a zirconium-based alloy, resulting in higher permeability of tritium through cladding to the reactor coolant.
Refractory Metals for Fuel Cladding
Refractory metals and alloys are well known for their extraordinary resistance to heat and wear. The key requirement to withstand high temperatures is a high melting point and stable mechanical properties (e.g., high hardness) even at high temperatures. The most common refractory metals include five elements: niobium and molybdenum of the fifth period and tantalum, tungsten, and rhenium of the sixth period. They share some properties, including a melting point above 2000 °C and high hardness at room temperature. Poor low-temperature fabricability and extreme oxidability at high temperatures are the main disadvantages of most refractory metals. The application of these metals requires a protective atmosphere or coating.
Zr-alloy lined Molybdenum Cladding.
In 2012, EPRI initiated an independent research project with conceptual designs of coated molybdenum alloy as an ATF cladding to achieve accident resistance to a temperature range of 1,200–1,500°C. Molybdenum (Mo) is a candidate because of its high melting point (2623°C) and high strength at elevated temperatures. At the same time, Mo and its alloys are known to be susceptible to forming volatile MoO3 in oxidizing environments at temperatures > 600°C. Therefore, this research program uses a composite design in which the Mo alloy cladding is covered with an outer protective coating of either a Zr-alloy or an Al-containing alloy.
The Zr-alloy lined Mo-cladding is anticipated to possess sufficient corrosion and hydriding resistance for the current fuel burnup limit and beyond. The fully metallic Mo–Zr and Mo–FeCrAl duplex claddings are anticipated to achieve accident tolerance by forming a protective oxide during an accident. The thin Zr-alloy coating will completely oxidize to ZrO2 as the temperature reaches 1,000°C or higher. The ZrO2 will maintain its integrity and stability with proper alloying and protect the underlining Mo alloy. A thin FeCrAl coating is highly corrosion resistant in LWR coolants due to the formation of a chromium-rich protective oxide, mainly Cr2O3. FeCrAl is highly corrosion resistant in high-temperature steam due to forming a thin aluminum-rich oxide, Al2O3. FeCrAl alloys consist mainly of iron, chromium (20–30%), and aluminium (4–7.5 %). These alloys are known under the trademark Kanthal, a family of iron-chromium-aluminium (FeCrAl) alloys used in a wide range of resistance and high-temperature applications.
Molybdenum is highly resistant to oxidation in high-purity or reducing steam. Therefore, the lined molybdenum cladding is anticipated to maintain good integrity in the event of steam ingress into a failed fuel rod and under a design-basis LOCA. If the outer coating is locally removed, such as grid-to-rod fretting, localized corrosion of molybdenum cladding may occur.
SiC and SiC/SiC-composite claddings
Silicon carbide is an exceedingly hard, synthetically produced crystalline compound of silicon and carbon, and its chemical formula is SiC. Silicon carbide has a Mohs hardness rating of 9, approaching that of a diamond. In addition to hardness, silicon carbide crystals have fracture characteristics that make them extremely useful in grinding wheels. Its high thermal conductivity, high-temperature strength, low thermal expansion, and resistance to a chemical reaction make silicon carbide valuable in manufacturing high-temperature applications and other refractories.
In the nuclear industry, silicon carbide composite material has been investigated for use as a replacement for zirconium alloy cladding in light water reactors. Silicon carbide (SiC) based ceramics, and their composites have superior high-temperature (HT) properties, excellent irradiation resistance, inherent low activation, and superior physical/chemical properties. The composite consists of SiC fibers wrapped around a SiC inner layer and surrounded by a SiC outer layer. Problems have been reported with the ability to join the pieces of the SiC composite.
SiC cladding is intended to provide groundbreaking safety margin improvements. SiC cladding reacts many orders of magnitude slower with water and steam than zirconium at critical temperatures (above 800°C), resulting in the minimal generation of heat and hydrogen in beyond-design-basis accident scenarios. The SiC-composite claddings and fuel components are expected to provide excellent passive safety features both in design-basis accidents and design extension conditions severe accidents (SAs). Moreover, the SiC/SiC composites are anticipated to provide additional benefits over the Zr-alloys, such as a reduced neutron absorption cross-section enabling a smaller uranium enrichment. These attractive features make the SiC composites one of the leading candidates for accident-tolerant LWR fuel cladding and core structures.
There are three main disadvantages of the SiC/SiC composite fuel clads:
- Fabrication. Fabrication of thin fuel clad requires further development. A technology for end-plug joining with gas tightness and adequate strength should also be developed because SiC ceramics cannot be welded.
- Tritium releases. There is a potential increase in tritium release into the reactor coolant. Tritium is produced as a fission product (FP). SiC does not react with hydrogen to form stable hydrides like a zirconium-based alloy, resulting in higher tritium permeability through the cladding to the reactor coolant. The choice of using a proper liner material could help mitigate this issue.
- SiC/SiC has significantly lower thermal conductivity than zirconium alloys. This fact negatively influences pellet centerline temperatures and also the coping time.
One possible SiC composite cladding has been developed by General Atomics. They are known as SiGA™ silicon-carbide (SiC) composite, in which the SiC matrix material is reinforced with flexible SiC fiber in the same way steel rebar reinforces concrete. This creates an extremely hard and durable material that can withstand the harshest reactor conditions.
Accident-tolerant control rods – ATCR
Control rods are an important safety system for nuclear reactors, and their prompt action and prompt response to the reactor are indispensable. Control rods are used for maintaining the desired state of fission reactions within a nuclear reactor (i.e., subcritical state, critical state, power changes). They constitute a key component of an emergency shutdown system (SCRAM).
Control rods are rods, plates, or tubes containing a neutron-absorbing material (material with high absorption cross-section for thermal neutron) such as boron, hafnium, cadmium, etc., used to control the power of a nuclear reactor. By absorbing neutrons, a control rod prevents the neutrons from causing further fissions.
Control rods usually constitute cluster control rod assemblies (PWR) and are inserted into guide thimbles within a nuclear fuel assembly. The absorbing material (e.g., pellets of Boron Carbide or Ag-In-Cd alloy) is protected by the cladding, usually made of stainless steel.
Nevertheless, the melting point of Ag-In-Cd alloy (~790 ̊C), the eutectic temperature of boron carbide (B4C) and Fe (~1150 ̊C), and the eutectic temperature of Fe and Zr (~950 ̊C) are lower than the temperature (≳1 200) at which Zr-alloy fuel cladding begins to be intensively oxidized under severe accident conditions. Accordingly, the control rods may melt and collapse before the reactor core is significantly damaged in the case of severe accidents.
The following inherent characteristics are required in accident tolerant control rods:
- The reactivity worth of ATCR should be comparable to or exceed that of conventional CR.
- The neutron-absorbing materials used in ATCR should have a sufficiently high melting point and high eutectic temperature with cladding to prevent breakage of the CRs before extensive fuel rod failure in a severe accident, thus avoiding uncontrollable recriticality even if unborated water is injected for emergency cooling of the core.
The main idea is to replace the conventional neutron-absorbing materials with proper ceramic materials that satisfy the above requirements. The candidate for a new absorber material for ATC includes gadolinium (Gd2O3), samarium (Sm2O3), europium (Eu2O3), dysprosium (Dy2O3), hafnium (HfO2). The melting point of these materials and the liquefaction temperature with Fe are higher than the rapid zirconium alloy oxidation temperature.
Improved UO2 fuel
Most PWRs use uranium fuel, which is in the form of uranium dioxide. Uranium dioxide is a black semiconducting solid with very low thermal conductivity. On the other hand, uranium dioxide has a very high melting point and has well-known behavior. The UO2 is pressed into pellets. These pellets are then sintered into the solid cylinder (with a height and diameter of about 1 centimeter, the height being greater than the diameter).
Regarding the improved UO2 fuel, this particular design was divided into two sub-concepts, such as:
- Doped UO2. Desirable attributes for accident-tolerant fuel (ATF) pellets include enhancing the retention of fission products (FPs) and minimizing pellet-cladding interaction. According to Westinghouse proposals, chromium (Cr2O3) and aluminum (Al2O3) doped UO2 pellet, known as our ADOPT pellet, achieves greater uranium efficiency through:
- Increased density of fissile material
- A higher creep rate than standard UO2 at high temperatures
- A higher thermal stability
- Reduced wash-out in the event of a fuel rod leaker
- Reduction of fission gas release in a transient scenario
- High-thermal conductivity UO2 (designed by adding metallic or ceramic dopant). Uranium dioxide is a black semiconducting solid with very low thermal conductivity. Thermal conductivity is one of the parameters which determine the fuel centerline temperature. This low thermal conductivity can result in localized overheating in the fuel centerline; therefore, this overheating must be avoided. The concept of cermet (ceramic-metallic) fuel for LWRs is considered. With a low volume fraction of highly conductive metallic additive, the CERMET fuel pellets present a higher conductivity than UO2 standard pellets, lowering the fuel temperature in normal operating conditions and increasing the margins with respect to fuel melting in case of an accident.
High-density fuel
Most metallic materials suggested for cladding to reduce steam oxidation present fairly large reactivity penalties compared to the traditional Zr-based claddings. These penalties can be compensated by either increasing the 235U enrichment and/or decreasing the cycle length. The fissile density in the pellet has to be increased to compensate for this without the previous concessions. The fissile density can be increased in several ways. One possible way is to increase the density of the material, and another one is to increase the metal to non-metal ratio in the metal compound fuels.
There are several proposed designs of high-density fuel, but it must be noted that all the high-density fuels are far from ready to be used as fuels in commercial light water reactors. The concepts include:
- Nitride Fuels
- Silicide Fuels
- Carbide Fuels
- Metallic Fuels
Uranium Silicide Fuel
Uranium silicide is an inorganic compound of uranium. It is one of the possible designs of accident-tolerant fuel pellet materials proposed. Advantages are a higher percentage of uranium and higher thermal conductivity. With a density of uranium silicide of 12.2 g/cm3 (vs. ), uranium silicide (U3Si2) boosts fuel economy. Uranium dioxide has a density of 10.97 g/cm3. Moreover, there is a surplus from its stoichiometric composition. Finally, there is about 17% higher uranium density than uranium dioxide. A direct replacement of UO2 with U3Si2 should enable a reactor to generate more energy from a set of fuel rods and provide more “coping time” in the case of severe accidents. Its thermal conductivity (~8.5 W/m.K at 300 K) is significantly higher than that of uranium dioxide at operating temperatures, and it increases as a function of temperature (uranium dioxide’s thermal conductivity decreases as a function of temperature). This thermal conductivity offsets its lower melting point, improving fuel operating and safety margins.
Westinghouse, the Idaho National Laboratory (INL), and the Los Alamos National Laboratory began developing and manufacturing uranium silicide and its composite fuels through DOE’s Accident Tolerant Fuel program. The improved thermal performance of U3Si2 compared to UO2 fuel allows the implementation of a more advanced cladding such as a SiC-SiC-composite, which besides the expected operational and safety benefits, also offers superior neutron economy and further fuel cycle cost savings relative to Zr-based claddings.
Encapsulated fuel – TRISO-SiC-composite pellets
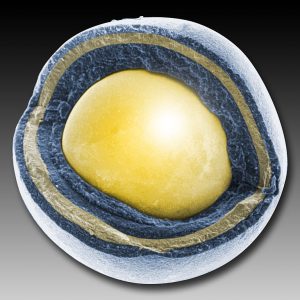
TRISO, TRI-structural ISO-tropic, is a type of micro fuel particle consisting of fissile material-bearing kernels coated with multiple layers of porous or dense carbon and silicon carbide. Historically, TRISO particles have been utilized in fuel elements consisting of spherical pebbles or hexagonal prismatic blocks with graphite used as a matrix and coating for the fuel element. Each particle acts as its containment system thanks to its triple-coated layers, allowing them to retain fission products under all reactor conditions. TRISO particles can withstand extreme temperatures well beyond the threshold of current nuclear fuels. TRISO-SiC-composite pellets consist of TRISO fuel particles embedded in a SiC matrix. Using SiC as a matrix instead of graphite improves the radiation tolerance of the fuel matrix while also enhancing FP retention. The TRISO-SiC-composite fuel is generally called a fully ceramic microencapsulated (FCM) fuel.
According to the NEA report, the TRISO-SiC fuel is conceived as a promising medium-term concept to replace current UO2 fuel pellets. It has superior safety characteristics relative to other fuel forms due to its multiple barriers to FP dispersion, high mechanical stability, and good thermal conductivity. A low fissile material loading density is the major issue for this concept. The combination of uranium enrichment up to the practical upper limit of LEU(~19.7% of 235-U) increases the fissile loading, increasing kernel-to-particle volume fraction and TRISO-packing fraction, and enlarging fuel pin diameter was proposed.
Silicon carbide is an exceedingly hard, synthetically produced crystalline compound of silicon and carbon. Its chemical formula is SiC. Silicon carbide has a Mohs hardness rating of 9, approaching that of a diamond. Its high thermal conductivity, high-temperature strength, low thermal expansion, and resistance to a chemical reaction make silicon carbide valuable in manufacturing high-temperature applications and other refractories. In the nuclear industry, silicon carbide composite material has been investigated for use as a replacement for zirconium alloy cladding in light water reactors. Silicon carbide (SiC) based ceramics, and their composites have superior high-temperature (HT) properties, excellent irradiation resistance, inherent low activation, and superior physical/chemical properties.