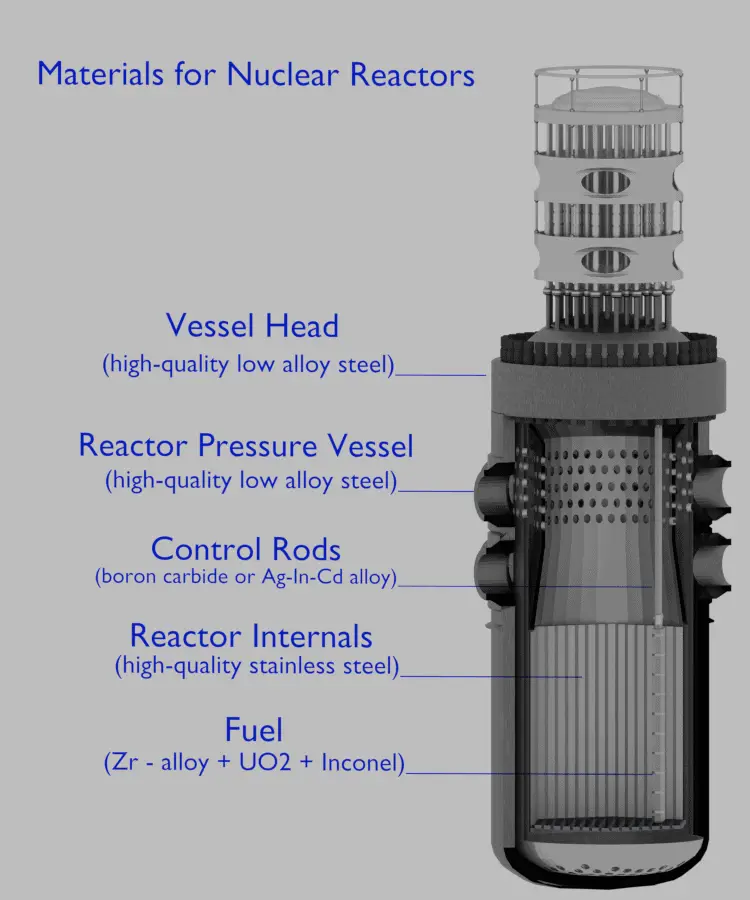
Pressurized water reactors use a reactor pressure vessel (RPV) to contain the nuclear fuel, moderator, control rods, and coolant. They are cooled and moderated by high-pressure liquid water (e.g., 16MPa). At this pressure, water boils at approximately 350°C (662°F), and inletnlet temperature of the water is about 290°C (554°F). The water (coolant) is heated in the reactor core to approximately 325°C (617°F) as the water flows through the core. As it can be seen, the reactor has approximately 25°C subcooled coolants (distance from the saturation).
The reactor pressure vessel is the pressure vessel containing the reactor core and other key reactor internals. It is a cylindrical vessel with a hemispherical bottom head and a flanged and gasketed upper head. The bottom head is welded to the cylindrical shell, while the top head is bolted to the cylindrical shell via the flanges. The top head is removable to allow for the refueling of the reactor during planned outages.
The body of the reactor vessel is constructed of high-quality low-alloy carbon steel, and all surfaces that come into contact with reactor coolant are clad with a minimum of about 3 to 10 mm of austenitic stainless steel (e.g., 304L) to minimize corrosion.
Low-carbon steel, also known as mild steel, is now the most common form of steel because its price is relatively low while it provides material properties that are acceptable for many applications. Low-carbon steel contains approximately 0.05–0.25% carbon making it malleable and ductile. Mild steel has a relatively low tensile strength but high toughness andt is easy to form. Special requirements for materials of reactor vessels include low activation capability (especially due to Co-60 formation). Examples of high-quality low-alloy carbon steels:
- SA-508 Gr.3 Cl.2 (low-alloy ferritic steel)
- 15Kh2NMFA (low-alloy ferritic steel)
Alloying Agents
Pure iron is too soft to be used for structure, but the addition of small quantities of other elements (carbon, manganese, or chromium, for instance) greatly increases its mechanical strength. The synergistic effect of alloying elements and heat treatment produces various microstructures and properties. The four major alloying elements are:
- Chromium. In these steels, chromium increases hardness and strength. Generally speaking, the concentration specified for most grades is approximately 2%, and this level appears to result in the best balance between hardness and toughness. Chromium plays an important role in the hardening mechanism and is considered irreplaceable. At higher temperatures, chromium contributes to increased strength.
- Nickel. Nickel does not form any carbide compounds in steel. It remains in solution in the ferrite, thus strengthening and toughening the ferrite phase.
- Molybdenum. When added to a steel, molybdenum (about 0.50-8.00%), ,makes it more resistant to high temperature. Molybdenum increases hardenability and strength, particularly at high temperatures, due to the high melting point molybdenum. Molybdenum is unique in the extent to which it increases steel’s high-temperature tensile and creeps strengths.
Austenitic stainless steels, which are used as a corrosion-resistant clad, contain between 16 and 25% of chromium and can also contain nitrogen in solution, both of which contribute to their relatively high corrosion resistance. The best-known grade is AISI 304 stainless, which contains chromium (between 15% and 20%) and nickel (between 2% and 10.5%) metals as the main non-iron constituents. 304 stainless steel has excellent resistance to a wide range of atmospheric environments and many corrosive media. Cold forming usually characterizes these alloys as ductile, weldable, and hardenable.
Type 304L stainless steel, widely used in the nuclear industry, is an extra-low carbon version of the 304 steel alloy. This grade has slightly lower mechanical properties than the standard 304 grade but is still widely used thanks to its versatility. The lower carbon content in 304L minimizes deleterious or harmful carbide precipitation due to welding. 304L can, therefore, be used “as welded” in severe corrosion environments, and it eliminates the need for annealing. Grade 304 has good oxidation resistance in intermittent service to 870°C and continuous service to 925 °C. Since grade 304L does not require post-weld annealing, it is extensively used in heavy gauge components. Examples of used stainless steels:
- Type 304L stainless steel
- Type 08Kh18N10T stainless steel
The reactor pressure vessels are the highest priority key components in nuclear power plants. The reactor pressure vessel houses the reactor core, and has direct safety significance because of its functione. During the operation of a nuclear power plant, the material of the reactor pressure vessel is exposed to neutron radiation (especially to fast neutrons), which results in localized embrittlement of the steel and welds in the area of the reactor core. To minimize such material degradation, radial neutron reflectors are installed around the reactor core. There are two basic types of neutron reflectors, the core baffle, and the heavy reflector. Due to higher atomic number density, heavy reflectors reduce neutron leakage (especially of fast neutrons) from the core more efficiently than core baffle. Since the reactor pressure vessel is considered irreplaceable, RPV’s aging effects can potentially be life-limiting conditions for a nuclear power plant.
Material Problems and Challenges of Nuclear Reactors
The main problems or rather challenges that must be taken into account when designing reactors are:
- Pressure and temperature stress with associated limits
- Pressure and Temperature (P/T) Limits
- Heat up and cooldown rates
- Low-temperature Overpressure Protection Limits
- Pressurized Thermal Shock
- Radiation Damage to Reactor Materials
- Corrosion
Special Reference: Reactor Pressure Vessel Status Report, U.S. NRC. NUREG-1511. Office of Nuclear Reactor Regulation U.S. Nuclear Regulatory Commission, Washington, 1994.