Classification of Turbines – steam supply and exhaust conditions
Steam turbines may be classified into different categories depending on their purpose and working pressures. The industrial usage of a turbine influences the initial and final conditions of steam. A pressure difference must exist between the steam supply and the exhaust for any steam turbine to operate. This classification includes:
- Condensing Steam Turbine,
- Back-pressure Steam Turbine,
- Reheat Steam Turbine,
- Turbine with Steam Extraction
Condensing Steam Turbine
Condensing steam turbines are most commonly found in thermal power plants. In a condensing steam turbine, the maximum amount of energy is extracted from the steam because there is a very high enthalpy difference between the initial (e.g., 6MPa; 275°C; x = 1) and final (e.g., 0.008MPa; 41.5°C; x = 0.9) conditions of steam. This is achieved by passing the exhaust steam into a condenser (called a surface condenser), which condenses the exhaust steam from the low-pressure stages of the main turbine (decreases the temperature and pressure of exhausted steam). The exhausted steam is condensed by passing over tubes containing water from the cooling system.
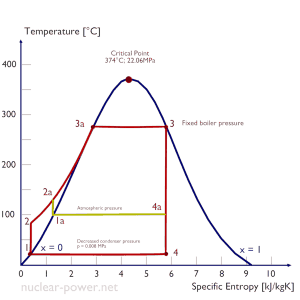
The goal of maintaining the lowest practical turbine exhaust pressure is a primary reason for including the condenser in a thermal power plant. The condenser provides a vacuum that maximizes the energy extracted from the steam, resulting in a significant increase in net work and thermal efficiency. But also this parameter (condenser pressure) has its engineering limits:
- Decreasing the turbine exhaust pressure decreases the vapor quality (or dryness fraction). At some point, the expansion must be ended to avoid damages that could be caused to blades of steam turbine by low-quality steam.
- Decreasing the turbine exhaust pressure significantly increases the specific volume of exhausted steam, which requires huge blades in the last rows of the low-pressure stage of the steam turbine.
In a typical condensing steam turbine, the exhausted steam condenses in the condenser, and it is at a pressure well below atmospheric (absolute pressure of 0.008 MPa, which corresponds to 41.5°C). This steam is in a partially condensed state (point F), typically of a quality near 90%. Note that the pressure inside the condenser is also dependent on the ambient atmospheric conditions:
- air temperature, pressure, and humidity in case of cooling into the atmosphere
- water temperature and the flow rate in case of cooling into a river or sea
An increase in the ambient temperature causes a proportional increase in pressure of exhausted steam (ΔT = 14°C is usually a constant); hence the thermal efficiency of the power conversion system decreases. In other words, the electrical output of a power plant may vary with ambient conditions, while the thermal power remains constant.
The pressure inside the condenser is given by the ambient air temperature (i.e., the temperature of water in the cooling system) and by steam ejectors or vacuum pumps, which pull the gases (non-condensable) from the surface condenser and eject them to the atmosphere.
The lowest feasible condenser pressure is the saturation pressure corresponding to the ambient temperature (e.g., the absolute pressure of 0.008 MPa, which corresponds to 41.5°C). Note that there is always a temperature difference between (around ΔT = 14°C) the condenser temperature and the ambient temperature, which originates from condensers’ finite size and efficiency.