How does a steam turbine work?
The thermal energy contained in the steam is converted to mechanical energy by expansion through the turbine. The expansion takes place through a series of fixed blades (nozzles) that orient the steam flow into high-speed jets. These jets contain significant kinetic energy, which is converted into shaft rotation by the bucket-like shaped rotor blades as the steam jet changes direction (see: Law of conversation of momentum). The steam jet, which is moving over the curved surface of the blade, exerts pressure on the blade owing to its centrifugal force. Each row of fixed nozzles and moving blades is called a stage. The blades rotate on the turbine rotor, and the fixed blades are concentrically arranged within the circular turbine casing.
In all turbines, the rotating blade velocity is proportional to the steam velocity passing over the blade. If the steam is expanded only in a single stage from the boiler pressure to the exhaust pressure, its velocity must be extremely high. But the typical main turbine in nuclear power plants, in which steam expands from pressures about 6 MPa to pressures about 0.008 MPa, operates at speeds about 3,000 RPM for 50 Hz systems for 2-pole generator (or 1500RPM for 4-pole generator), and 1800 RPM for 60 Hz systems for 4-pole generator (or 3600 RPM for 2-pole generator). A single-blade ring would require very large blades and approximately 30 000 RPM, which is too high for practical purposes.
Therefore most nuclear power plants operate a single-shaft turbine-generator that consists of one multi-stage HP turbine and three parallel multi-stage LP turbines, the main generator and an exciter. HP Turbine is usually a double-flow reaction turbine with about ten stages with shrouded blades and produces about 30-40% of the gross power output of the power plant unit. LP turbines are usually double-flow reaction turbines with about 5-8 stages (with shrouded blades and with free-standing blades of the last three stages). LP turbines produce approximately 60-70% of the gross power output of the power plant unit. Each turbine rotor is mounted on two bearings, i.e., there are double bearings between each turbine module.
In these turbines, the high-pressure stage receives steam (this steam is nearly saturated – x = 0.995 – point C at the figure; 6 MPa; 275.6°C) from a steam generator and exhausts it to moisture separator-reheater (point D). The steam must be reheated to avoid damages that could be caused to the blades of the steam turbine by low-quality steam. The reheater heats the steam (point D), and then the steam is directed to the low-pressure stage of the steam turbine, where it expands (point E to F). The exhausted steam then condenses in the condenser, and it is at a pressure well below atmospheric (absolute pressure of 0.008 MPa) and is in a partially condensed state (point F), typically of a quality near 90%.
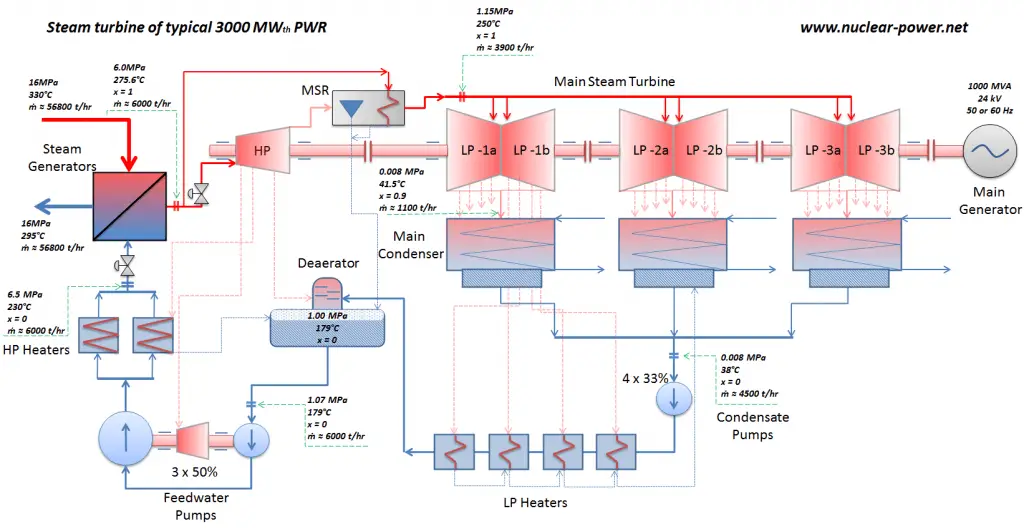