
Temperature in the pressurizer can be maintained at 350 °C (662 °F), which gives a subcooling margin (the difference between the pressurizer temperature and the highest temperature in the reactor core) of 30 °C. Subcooling margin is very important safety parameter of PWRs, since the boiling in the reactor core must be excluded. The basic design of the pressurized water reactor includes such requirement that the coolant (water) in the reactor coolant system must not boil. To achieve this, the coolant in the reactor coolant system is maintained at a pressure sufficiently high that boiling does not occur at the coolant temperatures experienced while the plant is operating or in an analyzed transient.
Functions
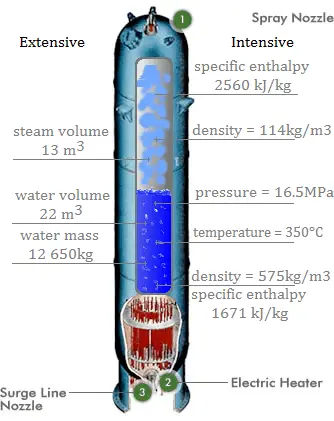
Pressure in the pressurizer is controlled by varying the temperature of the coolant in the pressurizer. For these purposes two systems are installed. Water spray system and electrical heaters system. Volume of the pressurizer (tens of cubic meters) is filled with water on saturation parameters and steam. The water spray system (relatively cool water – from cold leg) can decrease the pressure in the vessel by condensing the steam on water droplets sprayed in the vessel. On the other hand the submerged electrical heaters are designed to increase the pressure by evaporation the water in the vessel. Water pressure in a closed system tracks water temperature directly; as the temperature goes up, pressure goes up.
Over-pressure relief system
Part of the pressurizer system is an over-pressure relief system. In the event that pressurizer pressure exceeds a certain maximum, there is a relief valve called the pilot-operated relief valve (PORV) on top of the pressurizer which opens to allow steam from the steam bubble to leave the pressurizer in order to reduce the pressure in the pressurizer, thus leads to reduction of pressure in the whole system. This steam is routed to a large relief tank in the reactor containment building where it is cooled and condensed back into liquid and stored for later disposition. There is a finite volume to these tanks and if events deteriorate to the point where the tanks fill up, a secondary pressure relief device on the tank(s), often a rupture disc, allows the condensed reactor coolant to spill out onto the floor of the reactor containment building where it pools in sumps for later disposition.
The pressurizer is equipped also with safety valves system (“safety system”), which are also routed to the relief tank. The safety valves system is used to emergency pressure reduction during emergency conditions.
Water level monitoring
Since the reactor coolant system is completely flooded during normal operations, there is no point in monitoring coolant level in any of the other vessels. But early awareness of a reduction of coolant level (or a loss of coolant) is very important to the safety of the reactor core. The pressurizer is deliberately located high in the reactor containment building such that, if the pressurizer has sufficient coolant in it, one can be reasonably certain that all the other vessels of the reactor coolant system (which are below it) are fully flooded with coolant. There is therefore, a coolant level monitoring system on the pressurizer and it is the one reactor coolant system vessel that is normally not full of coolant.
Main components of pressurizer
- Pressure vessel
- Relief system. Consist of relief and safety valves and pressurized relief tank. The relief system is used to emergency pressure reduction during emergency conditions and the system.
- Water spray system. Consist of spray nozzles and spray line. The water spray system is used to pressure reduction during normal conditions and the system is used to mixing the coolant inside the pressurizer.
- Electrical heaters. The submerged electrical heaters are used to pressure increase during normal conditions.
- Surge line nozzle. Connects the pressurizer with the primary circuit.
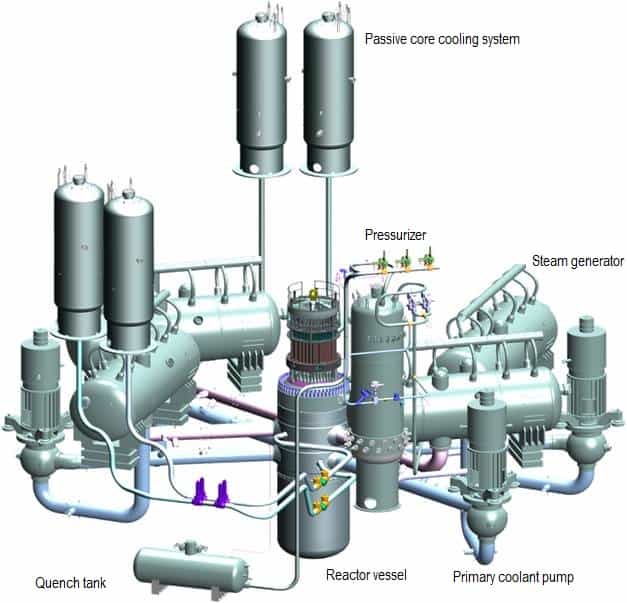
Source: http://www.bellona.ru/