Steam generators are heat exchangers used to convert feedwater into steam from heat produced in a nuclear reactor core. The steam produced drives the turbine. They are used in the most nuclear power plants, but there are many types according to the reactor type. The boiling water reactor does not require steam generators since the water boils directly in the reactor core. In other types of reactors, such as the pressurised heavy water reactors of the CANDU design, the primary fluid is heavy water. Liquid metal cooled reactors such as the Russian BN-600 reactor also use heat exchangers between a secondary sodium circuit and a tertiary water circuit.
Design of Steam Generator
To increase the amount of heat transferred and the power generated, the heat exchange surface must be maximalized. This is obtained by using tubes. Each steam generator can contain anywhere from 3,000 to 16,000 tubes, each about 19mm diameter.While the secondary fluid is always water, the reactor coolant (carbon dioxide, sodium, helium) depends on the reactor type. Where the coolant is pressurized water, two solutions have been adopted. In the first of these, the secondary water flows through straight tubes welded to tubesheets at both ends. This is the “once-through” type of steam generator. To eliminate the loads exerted on the tubesheets by differential thermal expansion between outside shell and the tubes, a second solutions is often employed. This alternative gives acope for thermal expansion by using U-tubes welded to a single tubesheet. The tubes carry the pressurized primary coolant and are surrounded by the secondary water, which is turned into steam.
There are two designes for U-tubes steam generators. Design with tube bundle arranged vertically and design with tube bundle arranged horizontally. Horizontal steam generators are used in the VVER type reactors. In commercial power plants, there are 2 to 6 steam generators per reactor; each steam generator (vertical design) can measure up to 70 feet (~21m) in height and weigh as much as 800 tons.
The materials that make up the steam generators and tubes are specially made and specifically designed to withstand the heat, high pressure and radiation. The water tubes also have to be able to resist corrosion from water for an extended period of time.
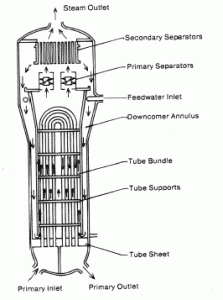
Operating conditions
The hot primary coolant (water 330°C; 626°F; 16MPa) is pumped into the steam generator through primary inlet. High pressure of primary coolant is used to keep the water in the liquid state. Boiling of the primary coolant shall not occur. The liquid water flows through hundreds or thousands of tubes (usually 1.9 cm in diameter) inside the steam generator. The feedwater (secondary circuit) is heated from ~260°C 500°F to the boiling point of that fluid (280°C; 536°F; 6,5MPa). Heat is transferred through the walls of these tubes to the lower pressure secondary coolant located on the secondary side of the exchanger where the coolant evaporates to pressurized steam (saturated steam 280°C; 536°F; 6,5 MPa). The pressurized steam leaves the steam generator through a steam outlet and continues to the steam turbine. The transfer of heat is accomplished without mixing the two fluids to prevent the secondary coolant from becoming radioactive. The primary coolant leaves (water 295°C; 563°F; 16MPa) the steam generator through primary outlet and continues through a cold leg to a reactor coolant pump and then into the reactor.
See also: Steam Tables
Moisture separation
A moisture separation is important to maintain the moisture content of the steam as low as possible to prevent damage to the turbine blading. The vertical steam generators must use multiple stage moisture separation. The horizontal separators can use the moisture separation, but it is not necessary, since the steam releases the two phase fluid much more slowly and the produced steam is generally without moisture.
The vertical steam generators use usually two stages of moisture separation. One stage causes the mixture to spin, which slings the water to the outside. The water is then drained back to be used to make more steam. The drier steam is routed to the second stage of separation. In this stage, the mixture is forced to make rapid changes in direction. Because of the steam’s ability to change direction and the water’s inability to change, the steam exits the steam generator, and the water is drained back for reuse. The two stage process of moisture removal is so efficient at removing the water that for every 100 pounds of steam that exits the steam generator, the water content is less than 0.25 pounds.
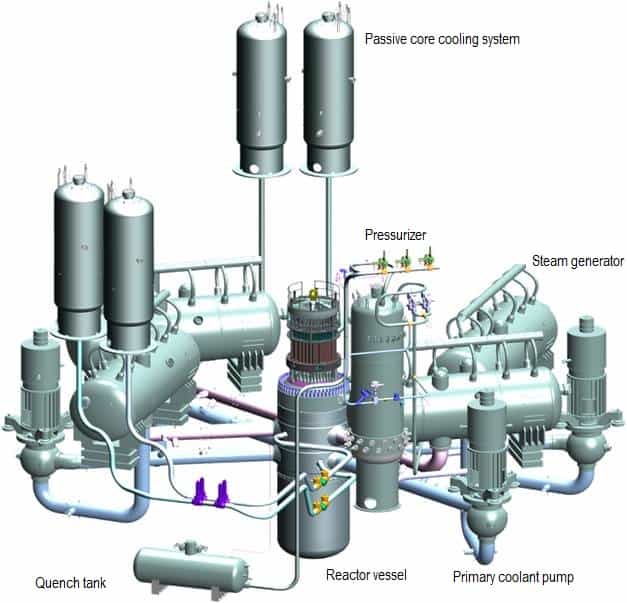
Source: http://www.bellona.ru/